Abrasive WheelsMole Abrasive
For a century Fratelli Guidetti has been associated with the Norton brand, this implies an established specialization in the abrasives sector, providing technical sales support, giving clear and practical feedback for choosing the most suitable product for the customer’s needs.
With thousands of products in stock, Norton establishes itself as a world leader in abrasives, offering innovative, functional and intuitive solutions for every market and process. Grinding, cutting, finishing on all materials even in the most complex and demanding applications.
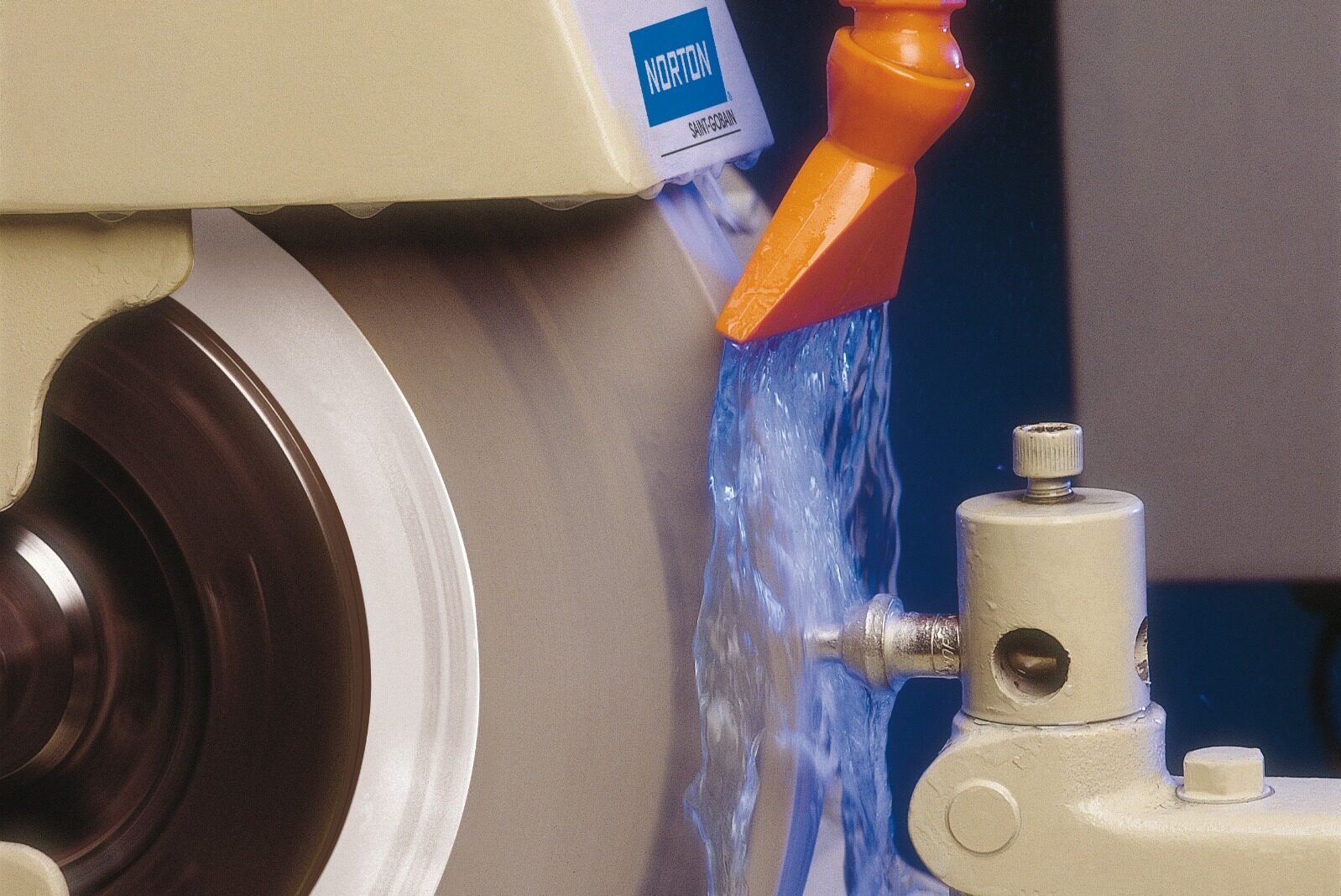
CYLINDRICAL GRINDING
Cylindrical grinding is used in the machining of cylindrical, conical or shaped surfaces. It is widely used in the machining of crankshafts, where machining is very complex and requires great precision. Norton offers a wide range of products that guarantee the best performance and precision on the workpiece.
New from Saint Gobain is the Quantum abrasive, which with its extreme sharpness and micro-fractured abrasive grains increases the productivity of the grinding process.
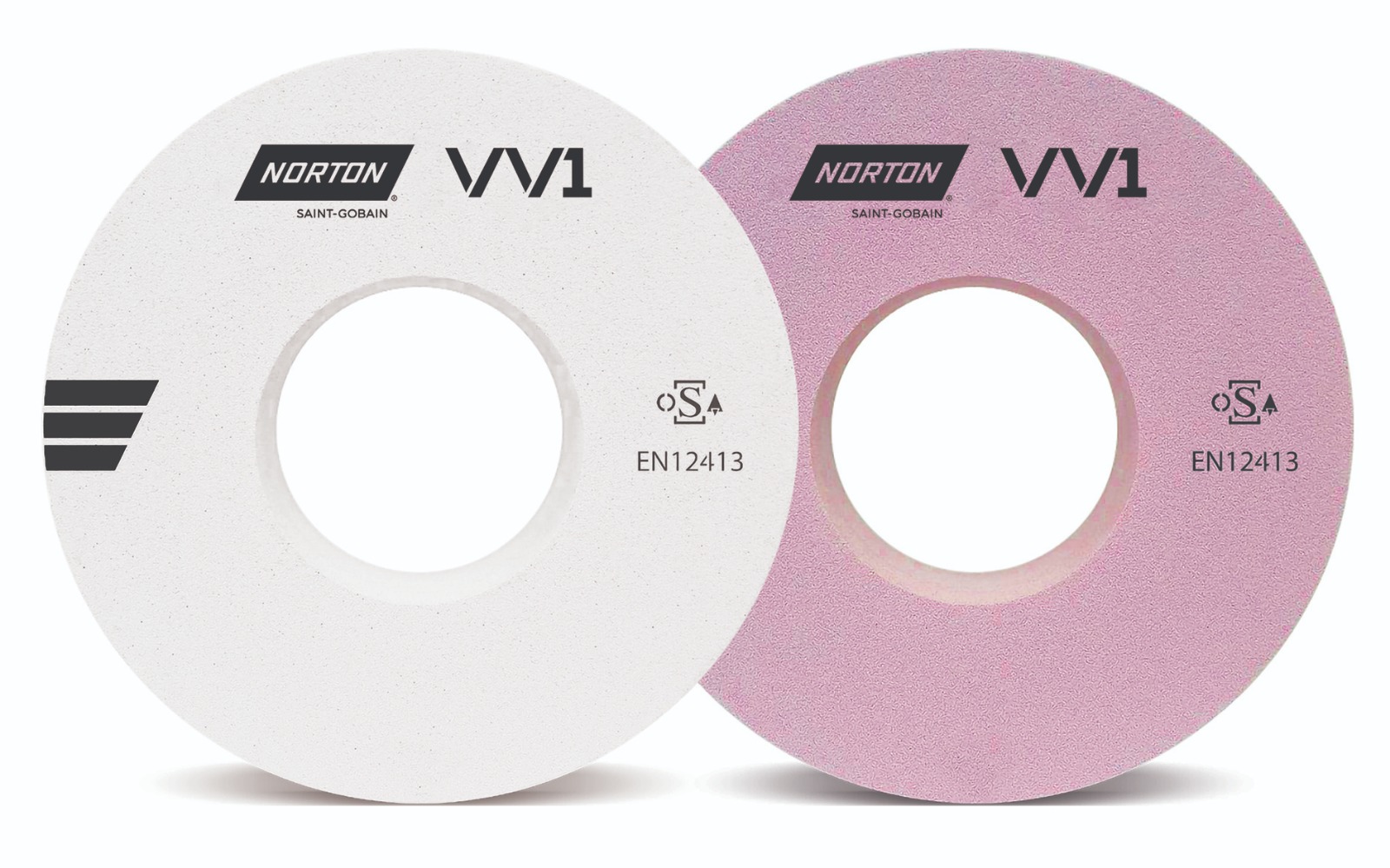
CENTERLESS GRINDING
When the workpieces to be machined change shape and size, this is where Centreless Grinding comes in, an operation consisting of two grinding wheels, an operating and a driving wheel.
The driving wheel, generally smaller, has the task of rotating the workpiece and pushing it against the operating wheel.
The operating wheel, larger than the driving wheel, has the task of grinding the workpiece.
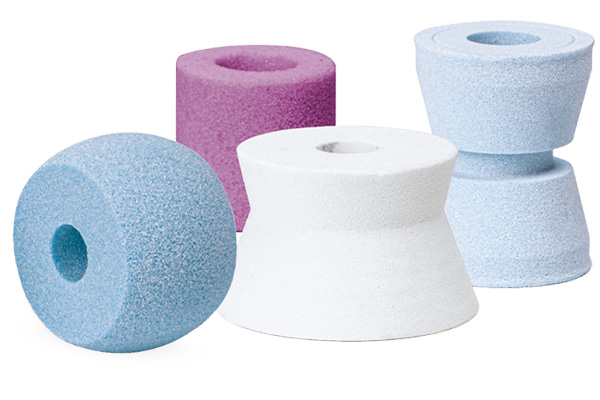
INTERNAL GRINDING
When the product to be ground is a bushing, a ring, or a cylinder, internal grinding takes place.
This operation is one of the most complex of grinding operations, requiring perfect calibration of the internal zone.
The grinding wheels, which are much smaller and generally equipped with very sharp abrasives, reach a speed of 30,000 revolutions per minute. The large number of revolutions and the high sharpness of the abrasive ensure that machining is very precise while maintaining the roughness and concentricity of the workpiece.
Norton offers a great product line for internal grinding, the flagship being the Ideal Prime range, which with its innovative combination of nanocrystalline ceramic grit and optimised bonds, is the solution for excellent grinding efficiency and longer tool life in high productivity markets requiring precision components.
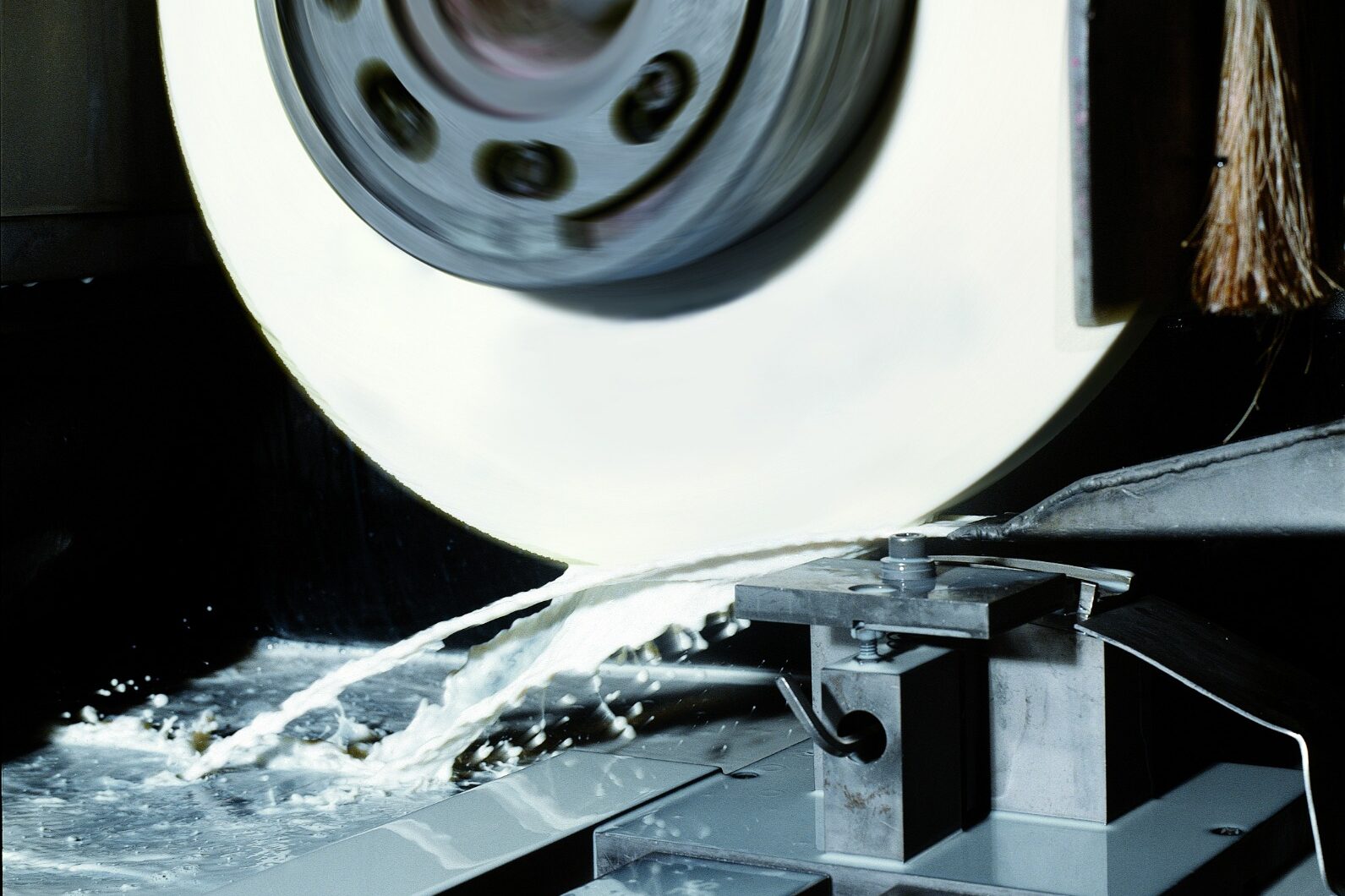
GRINDING IN PLAN
The term ‘surface grinding’ is used to describe the machining of flat or profiled surfaces where the grinding wheel moves and the workpiece is stationary, or vice versa.
Grinding operations range from heavy roughing to precision profile grinding. Other similar applications are disc grinding and creepfeed.
For all these applications, Norton has a wide range of grinding wheels (diamond or conventional) as well as segments and cylinders.
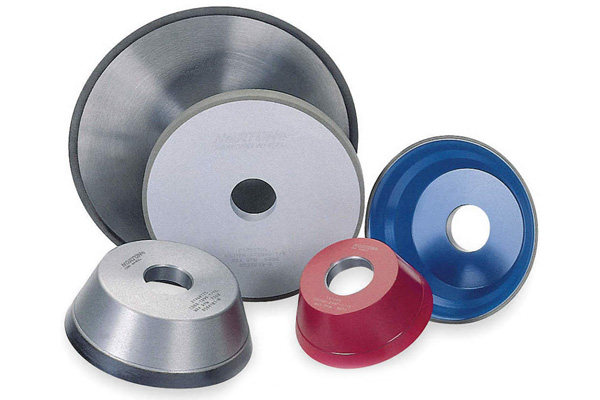
DIAMOND AND CBN GRINDING WHEELS FOR TOOLS
Diamond is the hardest material known to man, immediately followed by Cubic Boron Nitride (CBN). Due to their hardness, these materials are used in processes where very high precision is required, both in grinding and cutting.
Super Abrasive Grinding Wheels are used for grinding materials such as sintered carbides, super-hard steels, ceramics and glass. Norton provides high-performance, state-of-the-art super abrasive solutions for the tool industry, acting as an optimisation partner for various market applications
The values that guide us
KNOWLEDGE
The guideline, the competence, the engine
of innovation.
EXPERIENCE
As a result of field work and continuous research, for more than one hundred years.
COLLABORATION
Working together to find the most effective and appropriate solution.
CARE
Towards the human dimension and dignity of work. Attention and professionalism in relationships.
RELIABILITY
As a result of honesty and transparency, punctuality and guarantee.
SUSTAINABILITY
Accompanying in the transition towards more conscious and sustainable choices.